Sustainability
OUR NATURAL PRIORITY.
Sustainability comes naturally to people at Georgia-Pacific. Not only do our products help improve people’s lives, but we also operate in ways that enhance the quality of life in our communities, help ensure the economic stability of our company and help protect our environmental resources. Learn more about the various sustainable advantages of digital preprint for packaging.
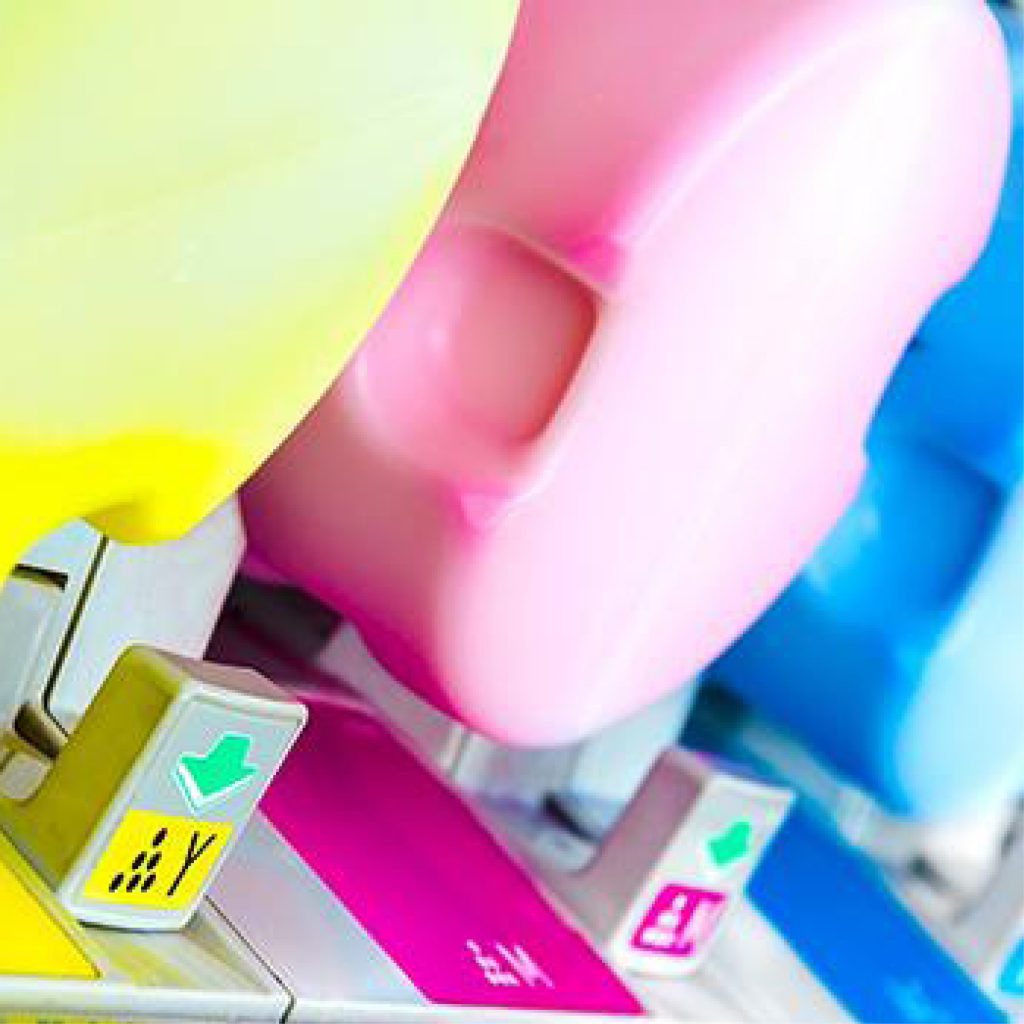
Aqueous Inks
HP A30 water-based pigment inks are designed to meet worldwide regulatory requirements and to address a broad range of health and environmental considerations throughout the entire life cycle of a print from production to disposal.
- Do not contain Hazardous Air Pollutants (HAPs). No hazard warning labels needed.
- Safe for printing on nonfood contact surfaces for secondary corrugated packaging, requiring no additional barriers.
- Pass odor and flavor test requirements for food packaging according to EN-1230-1,2.
- Very low VOC emissions when compared to typical offset lithography emissions.
- Are non-flammable and non-combustible; requires no special handling, storage, or transportation-related conditions.
- HP sponsored printhead recycling program (Drums/totes are recyclable/re-usable).
Aqueous Pre-Coat & Post-Coat
Aqueous substrate treatments maintain consistency with the ink.
- Hummingbird pre-coats substrates for aqueous inkjet receptivity in one of three ways to optimize print performance.
- Hummingbird uses only aqueous overprint varnishes (OPV) for protecting the ink, pre-coat and substrate.
- Pre-coat and post-coat OPV drums/totes are materially recyclable/re-usable.
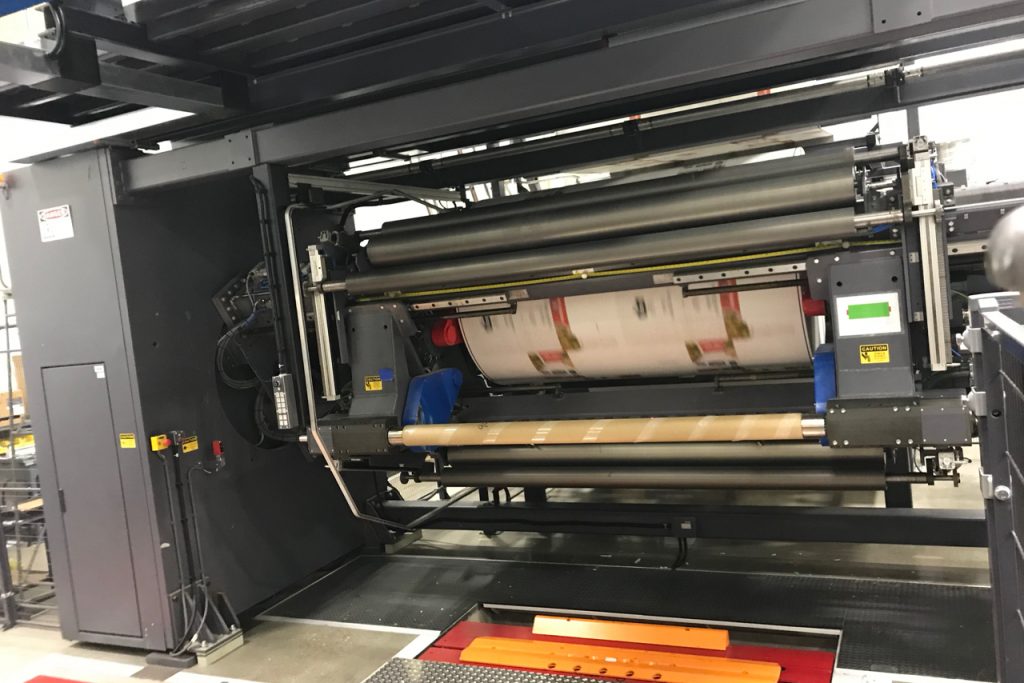
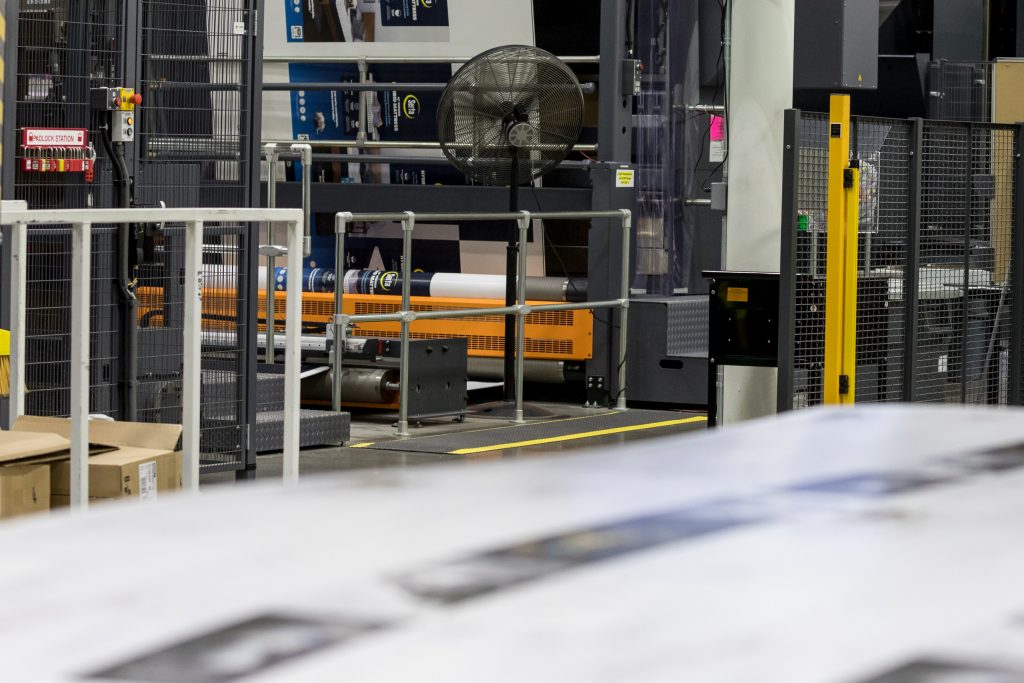
Reduced Production Waste
The paperboard packaging industry has a waste average of ~12 percent. With digital preprint, many traditional corrugated production processes can be enhanced to remove other hidden waste from the process, including:
- No longer needing litho labels applied to combined board, especially for large format boxes; thus reducing the number of corrugated layers and associated waste.
- Ability to shift to lighter weight print liners.
- Using lighter grades of printed liner substrates can help reduce your carbon footprint.
Reduced Obsolescence and
Improved Recyclability
With lower minimum order quantities than traditional print methods and the nimble ability to print only what you need when you need it, this enables:
- Reduced warehousing capacity needed for packaging inventory.
- Reduced inventory obsolescence and obsolete packaging waste.
Approximately 92 percent of all corrugated packaging is reclaimed for recycling each year.
Effective “de-inking” can also ensure the paper recycling process produces quality fiber in high yields.
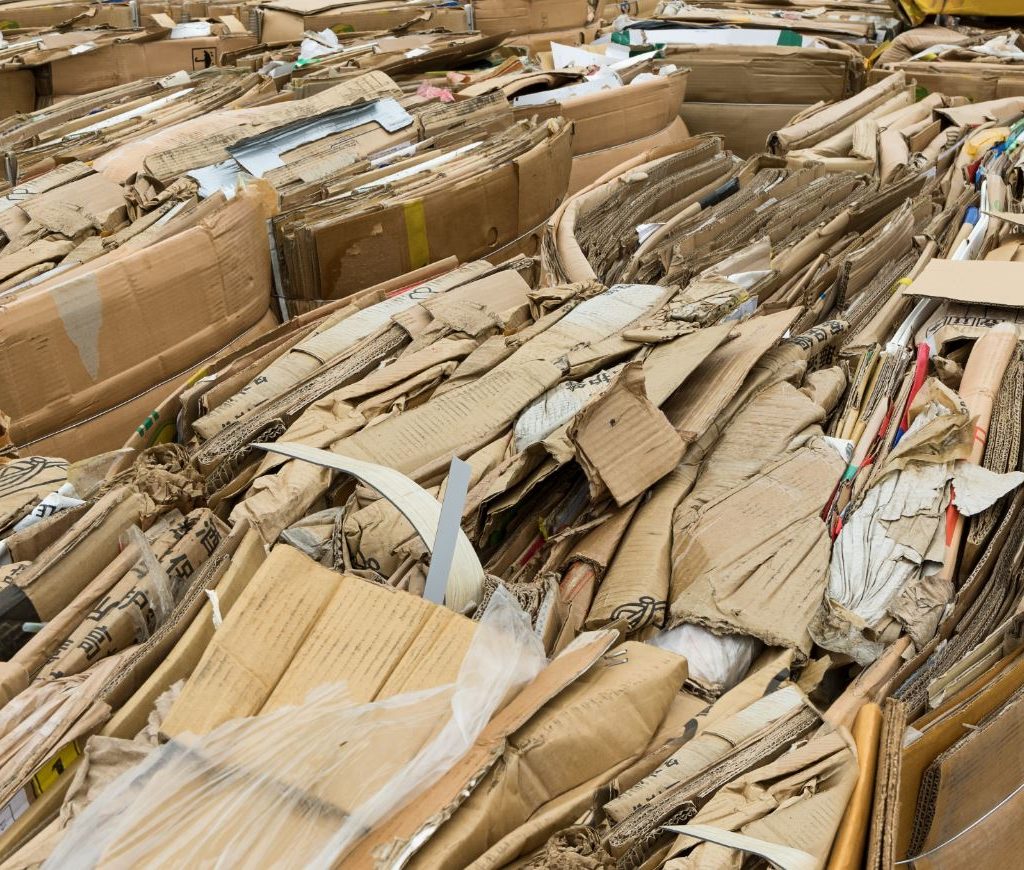
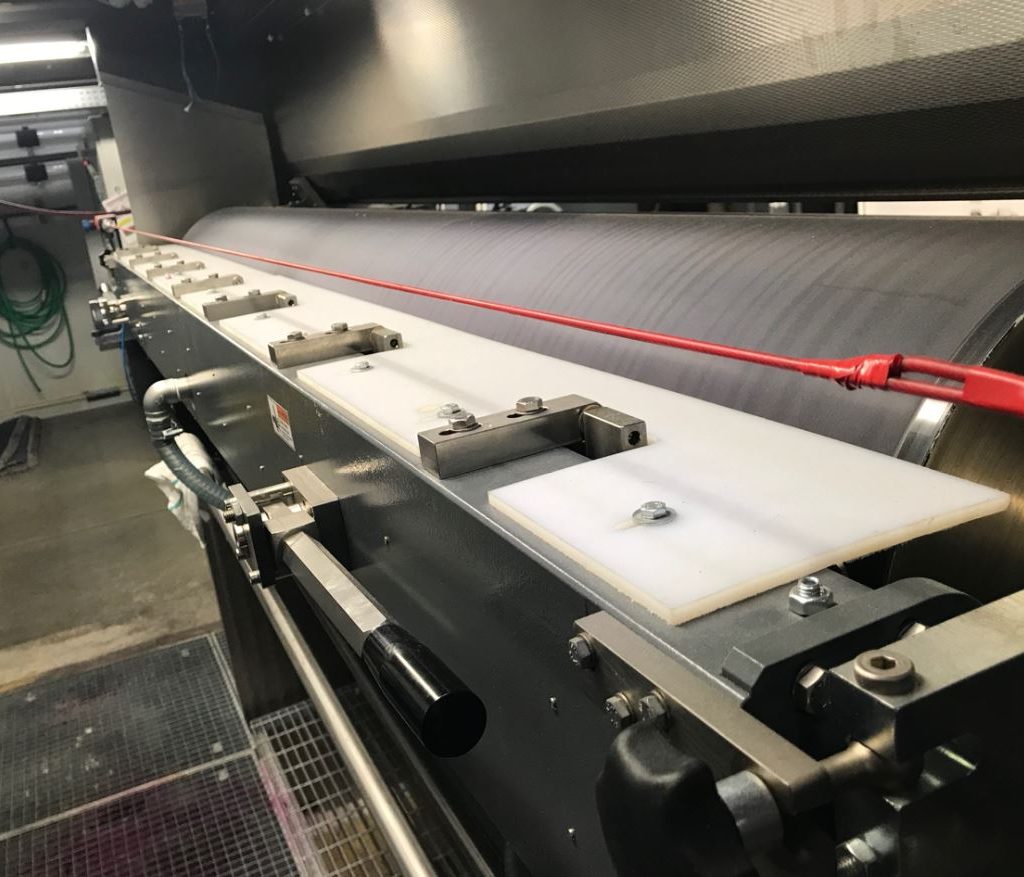
No Print Plates Required
Traditional print methods (flexography and litho lamination) require individual print plates to be produced for each color in a package’s design:
- A typical box, display, or label frequently requires multiple print plates in order to produce the desired print outcome.
- In most cases, these traditional print plates are not reusable over time.
For digital print, manufactured printing plates are not used:
- Subsequently reducing the heavy metals / plastics materials disposed in landfills for the pre-coat, ink, or post-coat (unless customer dictates OPV knockouts).
The Sustainable Forestry Initiative® (SFI®) certified sourcing label is proof GP Corrugated is using fiber from responsibly managed forests and legal sources.
The use of ColorPRO Technology enables high-quality results on lighter-weight grades of substrate and liners, which can translate into higher media usage efficiency.
See how Georgia-Pacific prioritizes sustainability across all of their businesses. Many GP products and facilities are recognized and/or certified by third-party groups.